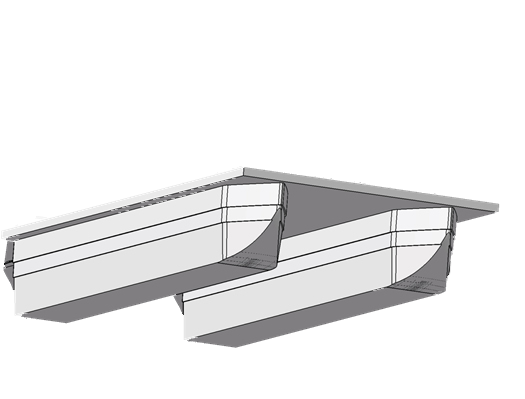
Endless Possibilities
Our Hull Platform Provides Strength and Flexibility to Suit Your Needs
There has never been a better platform for your own unique project because a large percentage of the strength of a boat is achieved through the hull. No expense has been spared designing and constructing the Honu Comfort Cats Hull, it was our goal to build a superior platform with zero wood to support the boat. This is ultimately where the strength and longevity of your boat is based and you won’t find another catamaran boat hull built to these standards. Every Honu Comfort cat hull is constructed with 10 individual watertight compartments with 2‘ x 2‘ removable bulkhead doors to access all watertight compartments for systems installation and repair. Every sealed compartment has a floor for mounting tanks or equipment with the exception of the stern compartment that has a 2-foot section with no floor to mount bilge pumps.
This Model Features
A catamaran hull and deck for your custom boat fabrication needs.
The Honu comfort catamaran sport model can also be purchased as a kit if you’re a handyman. The kit will include the Boat Hull, water tanks, waste tanks, and fuel tanks, all brackets to assemble the body and all body panels. This is a beautiful platform for you to build your own beautiful boat.
Every Honu Boat Hull is built with strength, accessibility, and convenience in mind. Fabrication begins with a solid one-piece fiberglass hull design pulled from a mold with a layup schedule approved by the United States Coast Guard. This solid one-piece construction process includes the sponsons (pontoon), the underside of the boat, and deck sidewalls creating superior strength and minimizing chances of flooding, or fracture. The next step is to use a strong marine adhesive and fiberglass to attach a 4 x 4 by 1/4 inch thick structural fiberglass box beam. This beam is installed down the centerline of each sponson as a keel for strength and a platform for the Sponson’s deck. The next step is to install 5 bulkheads constructed of high density closed cell foam encapsulated with fiberglass to the hull and keel.
The next step is to create 6 individual watertight compartments in each sponson by sealing in fiberglass and honeycomb deck panels to the keel, bulkheads and sponson sidewalls. Now a 4x6x1/4 inch structural fiberglass box beam is attached with strong marine adhesive, then fiberglassed around the perimeter of the deck creating a strong barrier for those occasional bumps to pilings or the dock.
Similar to the perimeter box beams the next step is to install 4x6x1/4 inch structural fiberglass box beams using strong marine adhesive. The beams are installed every 4 feet down the length of the hull and fiberglassed into place. The structural box beams are fiberglassed into place wherever there is contact with the hull. This method ties in the hull, support beams, and bulkheads for superior strength.
The next step is to apply strong marine adhesive to the top of all of the perimeter and horizontal structural beams. Then a two-piece floor deck cap is constructed in a mold with a three-quarter inch composite core. The deck cap is then installed and a rub rail is placed using number 10 marine stainless steel screws. This process further ties in the deck, rub rail, hull and structural box beams around the perimeter of the deck.